Caps and Closures Production: Selecting Between Injection and Compression Molding
In the dynamic, fast-changing world of beverage package design, selecting the right manufacturing method is crucial for creating high-quality caps and closures. Injection molding and Compression molding are two popular techniques for producing plastic caps and closures, and in this article, we will take a closer look at both methods, enabling you to make informed decisions to meet your specific requirements.
Let’s take a closer look at injection molding versus compression molding.
WHAT IS INJECTION MOLDING?
Injection molding is a versatile and efficient manufacturing process that involves injecting molten materials (resin) into a mold. The molten material is injected under high pressure into a closed mold cavity, where it cools and solidifies, taking the desired shape of the plastic part.
Injection molding enables the production of large volumes of identical parts with complex shapes and precise details. For this reason, injection molding has become a popular choice to produce caps and closures due to its remarkable flexibility, efficiency, and ability to consistently produce high-quality components. The beverage packaging industry, in particular, is making use of this manufacturing process to address sustainability trends and regulations, increase design flexibility, and streamline production and costs.
With injection molding, each process parameter is independently adjustable, allowing for a larger process window. This larger process window enables better adaptability to different raw materials and color masterbatches.

Advantages of Injection Molding
Complex Part Design Capabilities
Injection molding provides a higher degree of design freedom, enabling to create parts with undercuts, hinges, and advanced geometries used to enhance the consumer experience. This is particularly relevant with tethered caps.
Indeed, the complex geometry enables tethered caps with 180-degree openings on all necks and produces a pronounced clicking sound when users reach the end position, serving as a tactile cue.
No Post-Processing Requirements and Constant Bridge Quality
Injection molding also enables the ability to mold the tamper evident band with molded-in bridges eliminating the need for post-mold slitting and/or folding. As such, it reduces the required machinery and labor as well as the risks for quality concerns.
Molded-in bridges guarantee that the geometry of the bridges remains constant, with identical bridge size and position, cycle after cycle over the entire mold lifetime as there is no risk of wearing on the involved mold components. These conditions combined guarantee that the geometry of the bridges remains constant over time, guaranteeing part quality and consumer experience.
No Micro-Plastic Contamination
As there is no need for slitting with Molded-in bridge injected closures, there is also no generation of plastic dust linked to this step. This is a significant advantage for brands that are concerned with the potential contamination of microplastics that could end up in the beverage, food or medicine.
Lightweighting
Injection molding enables the production of lightweight parts without compromising quality or functionality. The process enables the optimization of wall thickness, resulting in lighter components that meet performance requirements. The elimination of the folded part of the closure reduces the part weight. Although it is true that best-in-class closures from both technologies are often at par in terms of weight, it is not uncommon to see injection molded closures be slightly lighter than compression molding.
Reduced Maintenance and Downtime
Once properly set up, an injection molding line can operate with minimal maintenance and downtime. Injection molding involves fewer components and tools in motion, which move at a considerably slower speed, leading to decreased maintenance needs overall resulting in less downtime.
Flexible Production
Injection molding is particularly interesting for converters that need to change closure types frequently: different neck finishes or from non-tethered to tethered. Changing the closure type is done by swapping the mold installed in the machine, which can be done within hours. The change from non-tethered to tethered requires the exchange of sliders only, which can be done without removing the mold from the machine within 1 hour.
Consistency and Process Robustness
Injection molding offers exceptional process control, resulting in consistent and repeatable part quality. The ability to closely monitor and adjust process parameters ensures that each part produced meets the desired specifications. Once the injection process is established, the process robustness allows for reliable and consistent production runs.
HyCAP™4 is the industry’s only fully integrated beverage closure injection molding system designed and built to work together for increased productivity, energy efficiency and ease of use.
WHAT IS COMPRESSION MOLDING?
Compression molding is a manufacturing process that involves the use of pressure to form preheated material into a desired shape. Unlike, injection molding where a multi-cavity mold produces many parts during each injection cycle, in compression molding the machine is composed of a carousel equipped with many single-cavity molds that produce one closure each. Compression molding involves placing a preheated molding material, known as a charge, into an open mold cavity. The mold is then closed, and pressure is applied to compress the material into the desired shape. The part is cooled until the mold is opened and the part is extracted from the mold.
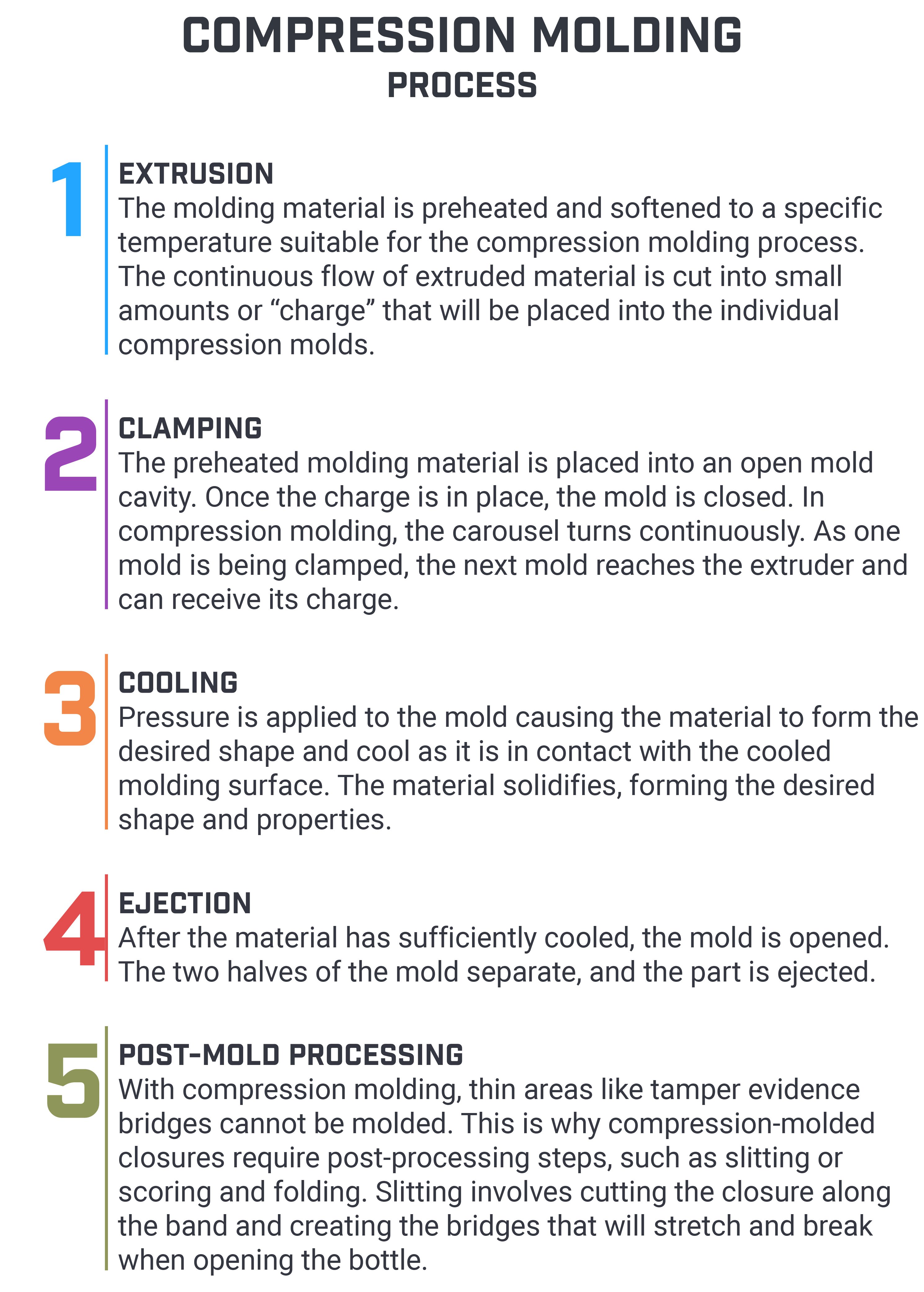
Advantages of Compression Molding
No Gate Mark
Compression molding does not require gates for material flow. This results in compression-molded parts having surface finish without visible gate marks.
Fast Color Changes
The extruder in a compression molding system feeds each mold directly without the need of a hot runner. Injection molding systems use a hot runner to distribute the molten resin from the injection unit to the mold cavities. The absence of the hot runner allows for faster color changes in compression molding.
Lower Energy Consumption
Compression molding works with lower resin temperatures, requiring less energy to warm up the material and to cool it down in the mold.
Lower Initial Equipment Investment
The initial investment costs for compression molding are lower compared to injection molding. This may benefit converters new to the closures business, but one should always consider the full cost of ownership.
Injection Molding vs Compression Molding
When comparing injection molding versus compression molding, it’s important to understand that the needs of your specific application should be the driving force behind your choice, as both processes have their benefits.
Let’s take a closer look at injection molding versus compression molding for caps and closures production.
Which process is more costly?
Compression molding typically has lower initial equipment cost than injection molding. However, resin costs are making up for more than 80% of the part cost. Energy and maintenance costs are the next biggest contributors.
When closure weights are equivalent, the closure cost has been found to be approximately 5% lower for compression molding in most cases. Resin cost is the primary cost driver, so a slight weight benefit to injection molding can offset the cost difference.
In cases where injection molding is marginally more expensive, the value of an improved consumer experience, through features like tethered closures with a 180-degree opening angle and audible and tactile cues, may well justify the increase in cost.
Although difficult to quantify, anyone considering investing in one of these technologies should also consider the cost linked to licensing fees, post-processing steps like slitting and folding when tethered closures are involved (i.e., the need for a system to orient the closure before slitting, increased cost of knives, advanced inspection systems, etc.).
Which process provides more flexibility?
One of the biggest advantages of injection molding is that it provides much more design flexibility and versatility. As mentioned above, injection molding may be preferred when undercuts or complex geometries are required. Design features like 180-degree opening and audible clicks, which have received positive feedback from major beverage brands have only been achieved with injection molding technology. The design freedom, and thus consumer experience that injection molding provides cannot be matched with compression molding.
Injection molding also provides flexibility in the production environment. Converters can use the same machine to produce a large variety of closures simply by exchanging the mold. This can be done within a few hours. The injection machine itself can be used to inject parts other than closures, resulting in a higher salvage value for the system.
In contrast, compression molding is better suited for simpler designs and in situations where the equipment is dedicated to one closure only and is loaded the entire year.
Which process is more efficient?
Injection molding offers streamlined, efficient and robust processes that contribute to enhanced production and overall efficiency. Planned maintenance is less demanding in injection molding compared to compression molding, given that there are less parts moving, and these parts are also moving more slowly.
Unlike compression molding, injection molding eliminates the need for additional post-production steps like slitting and folding and significantly minimizes the risk of scrap and dust,
In compression molding, tethered caps & closures need to be oriented prior to slitting and require a more complex slitting knife and process. To guarantee the quality of the slitting, the inspection process is also more complex.
Closures produced through injection molding, in contrast, are completely finished as they are released from the mold. All geometries are molded within the mold with high levels of repeatability.
While injection molding enables a molded-in-bridge, compression molding requires post-processing steps like slitting.
Which process enhances consumer safety?
The higher degree of design freedom provided by injection molded bands also translates into increased safety for end consumers, especially when tethered caps and closure designs are taken into account. Although tethered caps and closures are designed to remain attached to the bottle, they can be intentionally removed by consumers. The limited design options of slitting in compression molding, meanwhile, produce sharp edges and sturdy, spiky elements when the cap is separated from the band, as shown below. These factors have the potential to pose hazards for lip and finger injuries. Injection molded tethered caps and closures, on the other hand, have softer geometries that produce very thin and flexible arms, which are unlikely to cause injury.
How to Choose Between Injection Molding and Compression Molding
When comparing injection molding and compression molding, it’s clear that while compression molding offers advantages such as fast color changes and lower energy consumption, injection molding is a more versatile and efficient process overall. Injection molding provides design freedom and production flexibility to meet the needs of most beverage brands and converters.
However, to determine the best manufacturing method for your projects and applications, it’s important to evaluate their specific requirements and constraints. We encourage you to reach out to our subject matter experts, who can provide additional information and insights to enable you to make an informed decision.
Sources:
- RapidDirect. (2021). Compression molding vs injection molding: Which process is better?
- PETplanet PETinar. (2020). Tethered caps: An opportunity for compression and injection-molding?
- PR Newswire - Verified Market Research. (2019). Caps and Closures Market is Expected to Generate a Revenue of USD 93.25 Billion by 2030, Globally, at 4.78% CAGR
- Silgan Closures. (2018). Plastic Closures: Injection vs Compression - What Will You Choose?
- Plastics Today. (2010). Closure molding clash: Compression vs. injection